Over the recent years, TotalShield has seen a significant increase in inquiries related to battery testing, which can result in fire or explosion hazards. Customers often ask us questions like “What is your polycarbonate enclosures’ melting temperature?” or “What is your polycarbonate sheet’s fire resistance?”
Our response is a hallmark of engineering expertise: “Well, it depends.” The truth is, questions like these aren’t easy to answer because many variables are at play. Let’s take a deeper look at this.
Why polycarbonate’s melting point defies a singular value
The melting point of polycarbonate ranges between 295 °C to 315 °C, according to SyBridge Technologies. However, the exact melting point for different polycarbonate sheets can vary depending on various factors, including the specific thickness, grade, formulation, and the conditions under which they’re used.
For a more precise idea, let’s review the list of things our engineering team needs to know when designing a fire-resistant shielded enclosure or barrier:
- What size enclosure do you have, or are you looking for? Is it a 24” cubic benchtop enclosure or a 10’ x 10’ x 10’ large shield room?
- How close will the flame be to the shielded enclosure? Will the flame touch any polycarbonate panels directly, or will it occur within the enclosure but likely not touch the polycarbonate sheets?
- Will the flame be a quick, short burst or a prolonged event?
- Do you have a means of measuring the flame temperature at various locations within the polycarbonate enclosure?
- Have you performed and/or recorded any testing on this battery or impact application yet? If so, can we analyze some of that data?
- Most importantly, what is your impact threat? At TotalShield, we specialize in helping our customers determine the thickness of polycarbonate needed to adequately contain their impact threat, so knowing the level of the impact threat is essential.
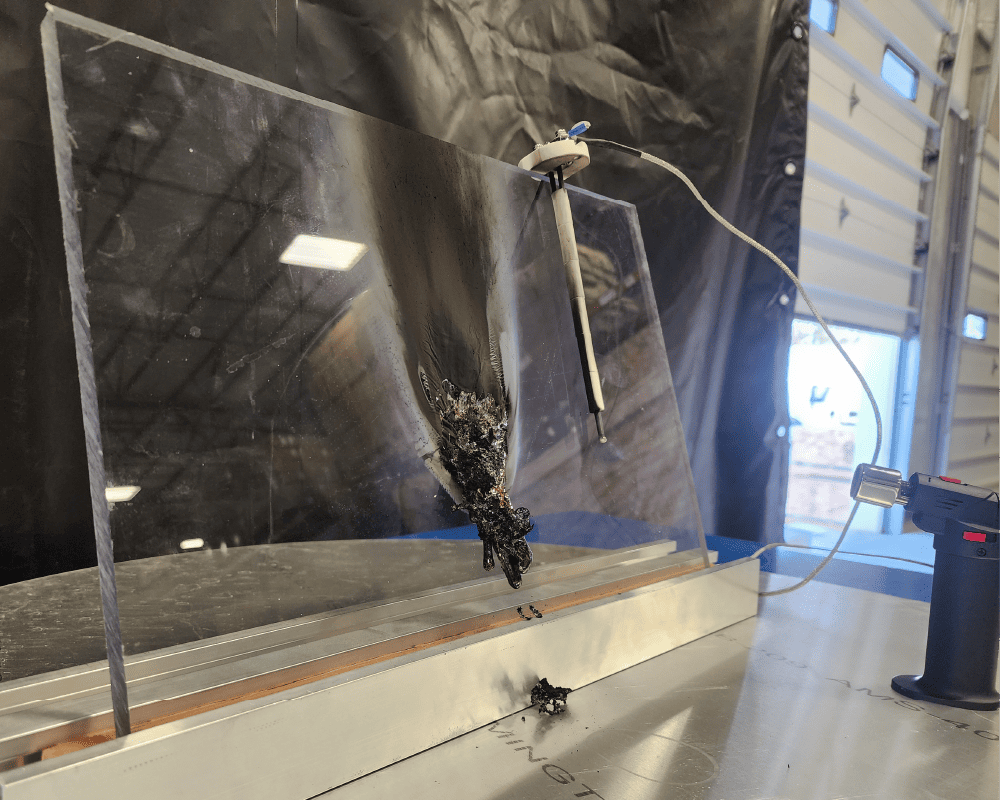
As you can see, determining the fire resistance of a polycarbonate-based shield enclosure involves various factors. That is why the answer to the question “What is the melting point of polycarbonate?” is not straightforward. Luckily for you, our engineering team loves to perform tests to gather more information.
Polycarbonate sheet’s fire resistance for different thickness
To better understand polycarbonate’s fire resistance, we’ll examine the three main thicknesses we use at TotalShield: 0.5”, 0.75”, and 1.25”. We use these thicknesses almost exclusively for our shielding solutions for the following reasons:
- We have empirically tested impact data for each, meaning we can certify our products against our proprietary Impact Testing Archive.
- Each thickness also has a Product Performance Rating section in their Material Specifications.
Examining those Product Performance Ratings helps to better understand the fire rating of each polycarbonate thickness.
0.5” thickness polycarbonate sheet
Our 0.5” sheet consists of one singular extruded piece of polycarbonate, whereas the other two are laminated.
This particular polycarbonate thickness has the most fire resistance and flammability data. Below, you’ll find a detailed list of the polycarbonate fire rating and flammability and performance rating criteria:
- ASTM D635 – Horizontal Burn, AEB ASTM D 635 in <1″
The material being tested meets the requirement of the test method ASTM D 635, with an “Average Extent of Burning” (AEB) of less than 1 inch. This indicates that the material does not burn extensively horizontally, with the extent of burning being minimal, less than 1 inch on average.
- Ignition Temperature, Self ASTM D 1929 °F 1022
ASTM D 1929 is a standard test method for determining the ignition temperature of plastics. The ignition temperature, also referred to as the autoignition temperature, is the minimum temperature at which a material will ignite spontaneously in the air without the presence of an external flame or ignition source.
When specifications mention “Ignition Temperature, Self ASTM D 1929 °F 1022”, it means that according to the ASTM D 1929 test method, the material in question has a self-ignition temperature of 1022 °F (approximately 550 °C).
- Ignition Temperature, Flash ASTM D 1929 °F 824
When specifications mention “Ignition Temperature, Flash ASTM D 1929 °F 824,” they refer to the flash ignition temperature determined according to the ASTM D 1929 standard test method.
The material in question has a flash ignition temperature of 824 °F (or approximately 440 °C), as determined by the ASTM D 1929 test method.
- Flame Class @ 0.060˝ UL 94 – HB
In the UL 94 test, specimens are subjected to a flame ignition source for a specified duration, and the burning characteristics are observed. The “HB” classification specifically means:
- The material burned slowly with a rate of burning less than or equal to 40 mm/min (approximately 1.57 inches/min) for thicknesses up to 3.2 mm (0.125 inches) or
- The material self-extinguished before reaching 100 mm (approximately 3.94 inches) from the point of ignition for thicknesses up to 13 mm (0.512 inches).
This classification indicates that while the material may burn when exposed to a flame, it does not propagate the flame excessively and is considered to have a relatively low flammability compared to higher classifications like V-0, V-1, or V-2.
- Flame Class @ 0.236˝ UL 94 – HB
The “HB” classification in UL 94, when specified at a thickness of 0.236 inches (6.0 mm), indicates that the material demonstrated a horizontal burning rate less than a specified value during testing.
This thickness in the UL 94 test implies a more substantial sample size than the standard thickness of 0.060 inches (1.5 mm). The “HB” classification at this thickness means that the material:
- Burned slowly with a rate of burning less than or equal to a certain threshold for the specified thickness or
- Self-extinguished before reaching a certain distance from the point of ignition.
- Combustibility Classification of “CC1”.
Per the International Code Council (ICC), Class CC1 indicates that:
“Plastic materials that have a burning extent of 1 inch (25 mm) or less when tested at a nominal thickness of 0.060 inch (1.5 mm), or in the thickness intended for use in accordance with ASTM D635.”
This means that the polycarbonate will self-extinguish between 0.4” and 1” thick. The Class CC1 specification also indicates that the material “shall have a self-ignition temperature of 650 °F (343 °C) or greater when tested in accordance with ASTM D1929.”
TotalShield’s polycarbonate fire resistance testing
We put 0.5” polycarbonate to the test in our own warehouse, performing in-house flame testing on various polycarbonate thicknesses using a butane torch.
Butane torches can reach up to 1300 °C (2600 °F). The torch was placed approximately 1” from the poly panel for approximately 10 minutes. Here you can find some of our observations:
- The polycarbonate sheet withstood the flame for nearly 10 minutes without full self-ignition or 100% material failure.
- After 10 minutes of the torch on the polycarbonate, the sheet had still not melted through its entire 0.5” thickness.
- We recorded temperatures at the flame side and the opposite side of the panel while the flame was burning and noticed remarkable temperature differences. For example, the flame was reading at approximately 1200 °F, and the rear side of the panel was cool enough to touch; there was very little radiation from the concentrated butane torch flame.
0.75” thickness polycarbonate sheet
Our 0.75” polycarbonate panel is a laminated cross-section of three different polycarbonate sheets—one layer of 0.5” thick polycarbonate interleaved by two 0.125” thick polycarbonate sheets. See the image below for the lamination cross-section.
The 0.75” polycarbonate also has a Combustibility Classification of “CC1” per the ICC.
We also tested this polycarbonate sheet during our in-house flame testing. We placed the butane torch approximately 1” away from the panel. Here is what we observed:
- The flame burned through the 0.125” lamination within approximately 1 minute, resulting in increased flame and charring from the adhesive bonding layer between the 0.125” sheet and the 0.5” sheet. We expected this might happen.
- After approximately 8 minutes, the 0.125” layer completely melted through, but the back 0.125” appeared not to have been damaged. The 0.5” layer was melted through approximately 50% (so ~0.25” melted). We could not record for 10 minutes as the torch ran out of butane fuel at roughly 8 minutes.
- The highest thermocouple reading we were able to record during the rest was approximately 1200 °F.
1.25” thickness polycarbonate sheet
This is one of our most robust options and is used primarily for high-impact applications such as high-impact ballistics (i.e., small projectiles traveling at very high speeds), high-pressure testing (i.e., stored energy in a pressure vessel), and containing explosive loads (i.e., bombs, explosives, etc.).
All the mentioned are the primary ways we utilize the 1.25” polycarbonate for unique customer applications.
The 1.25” poly is also a laminate, similar to the 0.75” polycarbonate. This sheet’s thickness also has a Combustibility Classification of “CC1”, per the ICC.
While we didn’t put the 1.25” sheet to a flame test, we assume that it would behave similarly to the 0.75” poly sheet, as the 1.25” consists of multiple laminations of polycarbonate that are glued together with a bonding adhesive.
Polycarbonate thermal capabilities and other benefits
Some of the polycarbonate’s thermal properties are the following:
- Heat resistance: We confirmed during our in-house testing that polycarbonate has good heat resistance and can withstand high temperatures without significant degradation.
- Long-term use temperature: Polycarbonate can be used at temperatures up to 130 °C (266 °F) for long periods.
- Heat deflection temperature: Polycarbonate’s heat deflection temperature is 279 °F (137 °C) at 0.45 MPa.
- Thermal conductivity: Polycarbonate’s thermal conductivity is 0.19 W/(m.k), which is very low compared to metals.
“Unlike glass, polycarbonate can withstand extreme temperatures, making it safer to use in building construction, and household items. Polycarbonate can be exposed to temperatures around 270 degrees for several hours or sudden bursts of heat up to 1166 degrees without distortion, breakage, or absorption of heat. Traditional glass can’t withstand high temperatures and can absorb heat, making it impossible to touch and increasing the chances of it breaking.”
Benefits of polycarbonate shielded enclosures
With its exceptional high-impact and fire resistance, polycarbonate stands out as an ideal choice for battery testing enclosures. Its high self-ignition temperature surpasses materials such as acrylic, wood, or other light-transmitting plastics in enduring high temperatures over prolonged periods.
Polycarbonate’s transparency facilitates a crucial aspect for customers: It allows them to observe their testing activities within an enclosed space, be it an explosion containment box or a walk-in room. Such visibility proves invaluable in lithium-ion battery testing, enabling customers to understand better and monitor the behavior of their batteries under test.
Additionally, polycarbonate’s lightweight characteristic offers a distinct advantage over steel plates. For instance, a 0.5” polycarbonate sheet weighs approximately 3 lb/SF, and 0.25” thick steel weighs approximately 10 lb/SF.
Considering our standard shield panel size is approximately 4’ x 4’, comparing the weight of a 4’x4’ shield panel in 0.5” polycarbonate against 0.25” steel reveals a substantial weight difference of nearly 112 lbs.
Polycarbonate vs. acrylic
For several reasons, polycarbonate is a better alternative when considering polycarbonate versus acrylic for shielding solutions.
Acrylic falls short in terms of flame and fire resistance, making it less suitable for environments where fire safety is a priority. When it comes to impact resistance, polycarbonate also outshines acrylic by a significant margin, boasting 30 times the impact resistance of acrylic.
Polycarbonate vs. steel
It’s common for our customers to request replacing polycarbonate with steel panels due to their superior fire resistance, but it’s essential to weigh the pros and cons of each material carefully.
While steel indeed offers enhanced fire resistance, this advantage comes with significant drawbacks. Unlike polycarbonate, steel is opaque, depriving users of the ability to observe tests inside the enclosure.
Steel is also much heavier than polycarbonate, which poses practical challenges. It is cumbersome to handle and lift compared to lightweight polycarbonate panels.
We offer alternative solutions if you are searching for a material that combines impact-resistant lightweight construction and doesn’t require transparency.
TotalShield’s custom battery testing enclosures
When it comes to custom shielding solutions, TotalShield offers a distinctive approach that prioritizes safety, versatility, durability, and a tailored enclosure to meet our clients’ unique needs.
One of the standout features is our Proprietary Impact Tested Framing System. Our bolted strut frame panel, engineered to capture polycarbonate, allows for effortless removal and replacement. This means that in the event of flame exposure or damage from high-impact incidents, replacing the polycarbonate sheet becomes a straightforward task without having to replace the entire enclosure. This feature increases the cost-effectiveness and efficiency of our solutions.
Additionally, our specialization lies in crafting highly customized enclosures. Consider the lithium-ion battery testing walk-in chamber and primary containment enclosures we designed for a customer:
The accessibility on all four sides ensures optimal viewing and easy access for testing procedures. The polycarbonate panels are designed to be sacrificial so that they can be easily replaced if damaged. This level of customization exemplifies our commitment to meeting diverse clients’ needs.
In our walk-in shield room applications, we offer seamless integration of fire suppression systems into the ceiling. These large enclosures are meticulously designed with modular shield panels featuring bolted connections.
In the image below, you can see how we integrate fire suppression tanks into the ceiling, showcasing our dedication to safety and functionality. For reference, that tank is mounted into a ceiling panel in an 8’ x 8’ x 8’ shield room.
As you can see, drawing on our extensive expertise, we craft shielding products tailored to withstand diverse impact threats. By engaging in rigorous testing and collaborating with third-party partners and subject-matter experts, we determine the ideal polycarbonate thickness specific to each testing application.
Past collaborations with research laboratories have been instrumental in comprehending customers’ worst-case impact threat scenarios. This allows us to design a shielding solution rated to contain your impact and certified against our proprietary Impact Testing Archive.
Choosing TotalShield guarantees not only top-tier containment enclosures but also a fully customized solution tailored to your specific needs and backed by a commitment to safety. Get in touch with us so one of our engineers can start working on your next project!